Reactive vs Preventive Maintenance
In facility management, most maintenance tasks are categorized as either “reactive” or “preventive.” It’s important to know the difference between the two, since the most successful facilities departments maintain a healthy balance between reactive and preventive maintenance. Even if you have an amazing preventive plan things can always happen.
In this blog, we’ll explain the difference between reactive maintenance and preventive maintenance and provide you with several resources to help you implement a strong PM program of your own. Let’s start by taking a look at the concept of reactive maintenance.
WHAT IS REACTIVE MAINTENANCE?
A reactive approach to facility management requires something to go wrong or break down before the issue gains attention. When an asset malfunctions, a maintenance technician will identify the issue that occurred and take steps to restore the asset to operational condition.
Some maintenance strategies, such as run-to-failure, purposely create reactive work. There are several good reasons for have a run-to-failure maintenance strategy for certain assets, such as small or non-critical assets that will have minimal financial impact when they break. However, if maintenance issues begin to pile up facility teams can become overwhelmed quickly. As this backlog piles up, repair costs can multiply and worsen over time.
Reactive Maintenance at a Glance
- Approach is crisis-based
- Chaotic execution of work responsibilities
- Frequent equipment failures
- Unplanned downtime due to equipment failure
- Delays in service and maintenance calls
- Increased costs due to broken building components
- Heavily people-dependent due to increased labor costs
Most money saved from reactive maintenance is negated, as it must be spent on unexpected breakdown repairs and parts replacements. Therefore, it’s a good idea to invest in a solid preventive maintenance program at your facility. Here’s how preventive maintenance differs from reactive maintenance.
WHAT IS PREVENTIVE MAINTENANCE?
Conversely, a preventive approach to facility management involves foresight and identifies a crisis before it happens. Real-time measurements are taken to predict system degradation and mechanical failure. As a result, negative consequences are minimized.
A preventive maintenance program may have contingencies in place in the event of a breakdown, such as backup generators for power outages or spare parts for immediate asset repair. Machinery is actively monitored and maintained to ensure optimal functionality. The most notable results of preventive maintenance are extended life of critical assets, reduced downtime and increased team productivity.
Preventive Maintenance at a Glance
- Approach is preparation-based
- Organized execution of work responsibilities
- Fully functional equipment and building components
- Longer life expectancy of critical equipment
- Greater cost savings in maintenance
- Improved worker and environmental safety
- Faster response times to service and maintenance calls
- Upgraded facilities and improved preventive maintenance
Preventive maintenance offers a variety of benefits over reactive maintenance. Saving money is a big advantage, but an even greater one is knowing your team is safe on the job. Preventive maintenance reduces risk and danger in your facility, since dangerous equipment is constantly monitored, inspected and serviced. Safe equipment can lead to higher employee satisfaction and fewer workplace injury claims, a win-win for everyone involved.
Learn More about Preventive Maintenance
Call Enviro US A today at 866-564-1414 or email info@envirousa.com. Here at Enviro USA we can create a customized building maintenance plan for your exact needs.
Enviro USA has over 27 years experience and highly trained technicians that are available 24 hours a day 7 days a week!
“Building Care Made Easy”
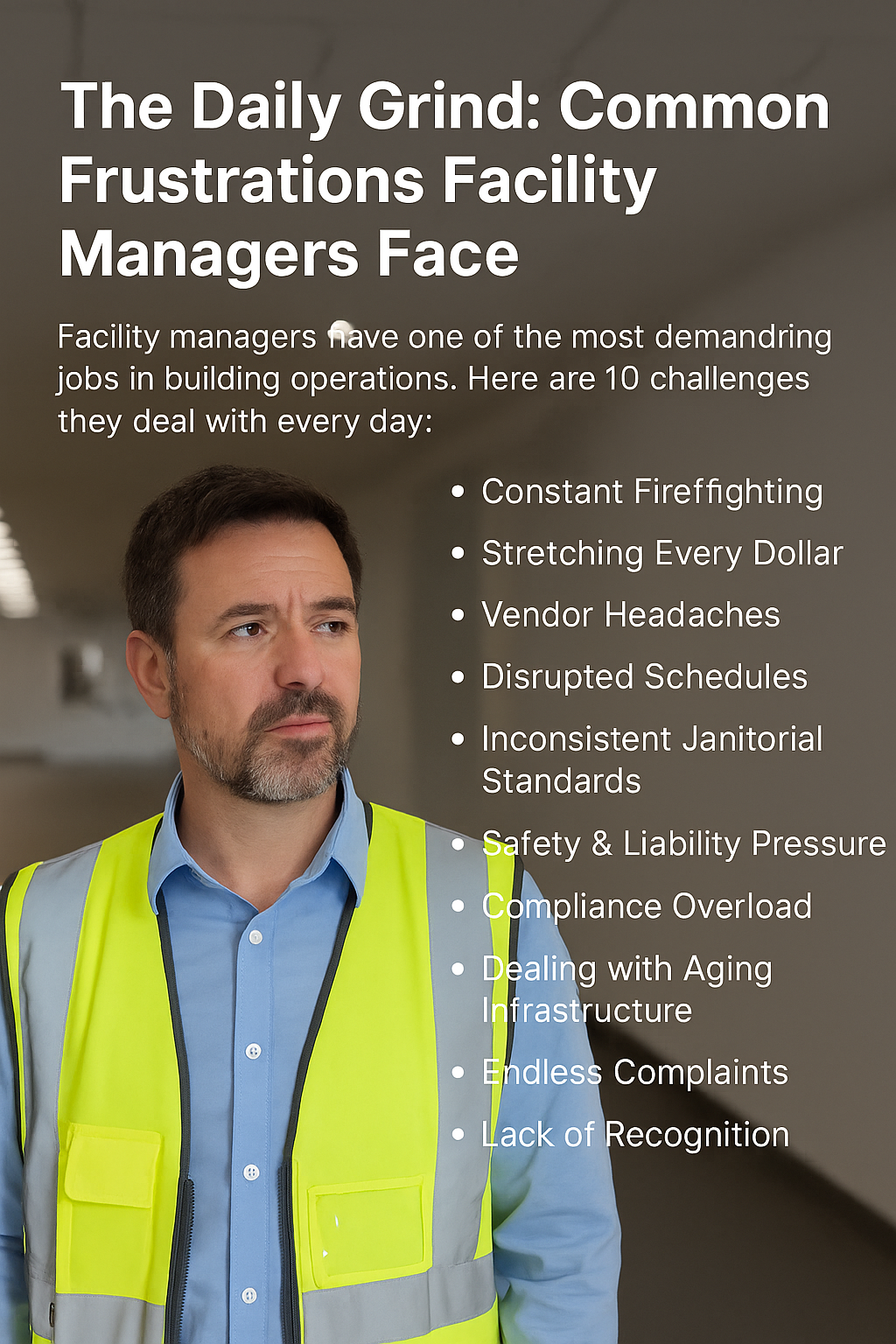
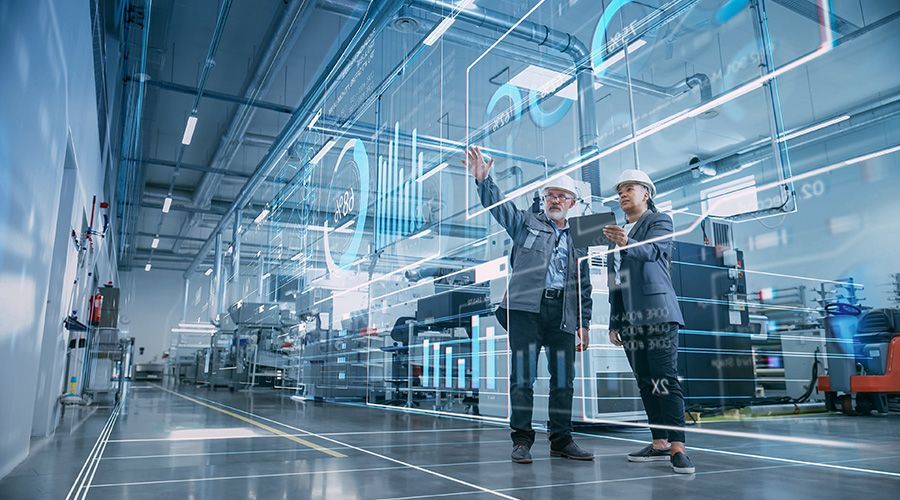
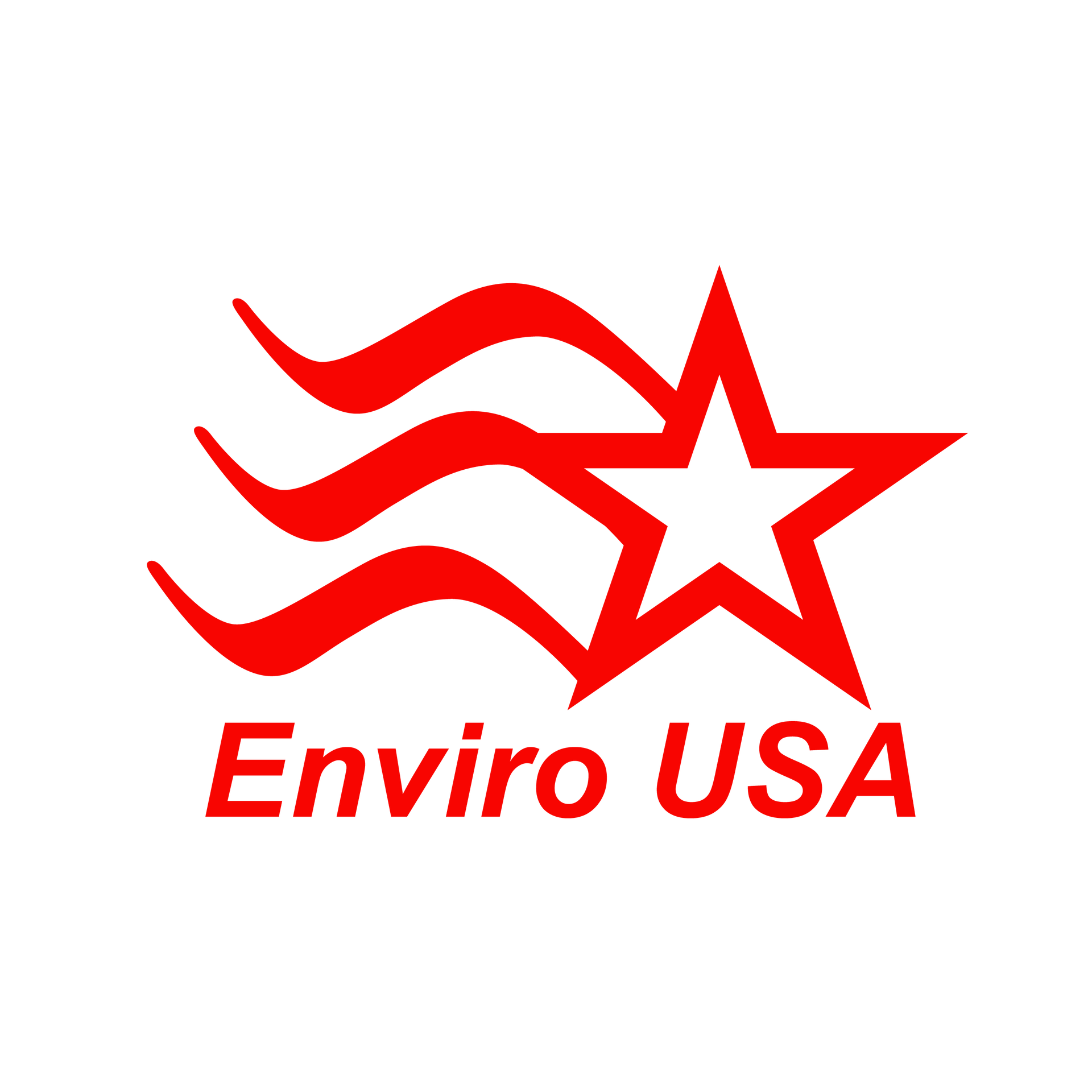

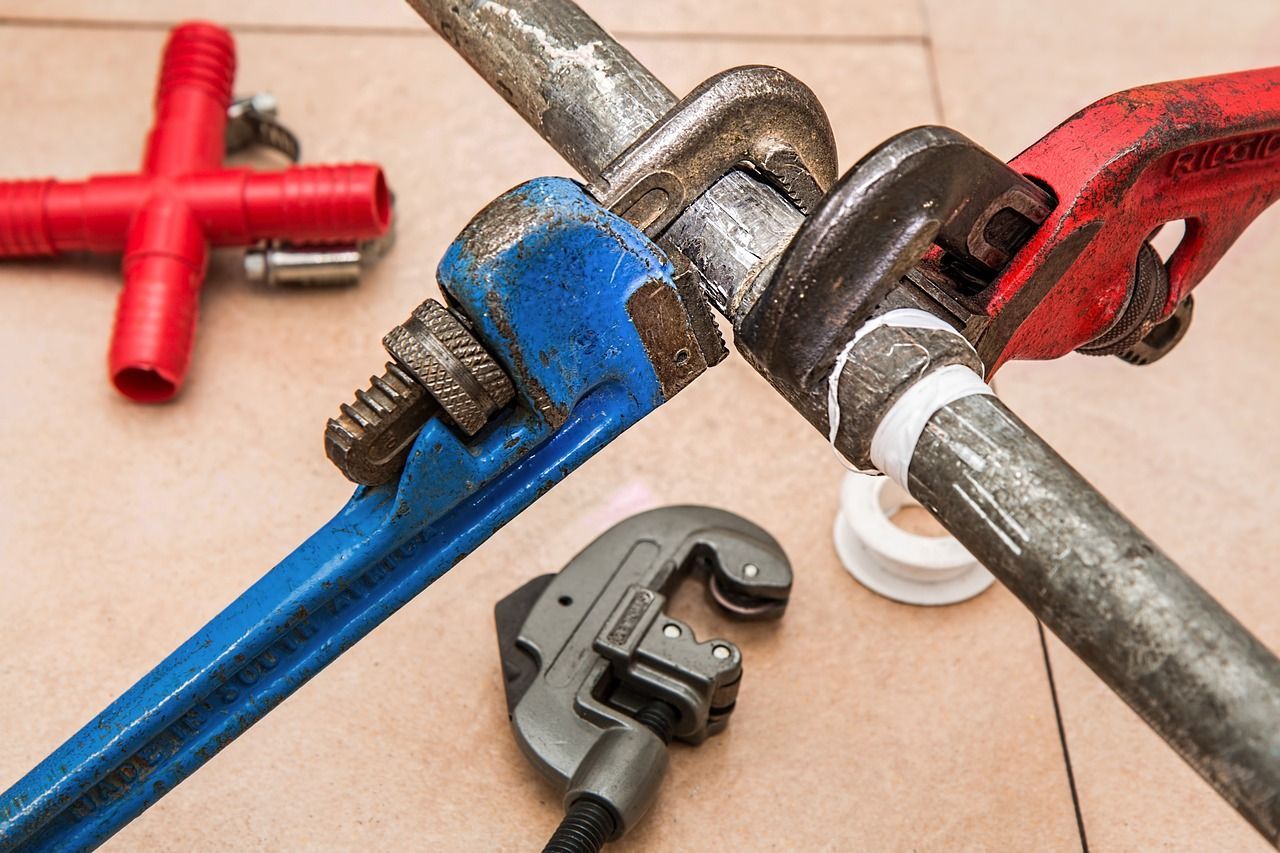
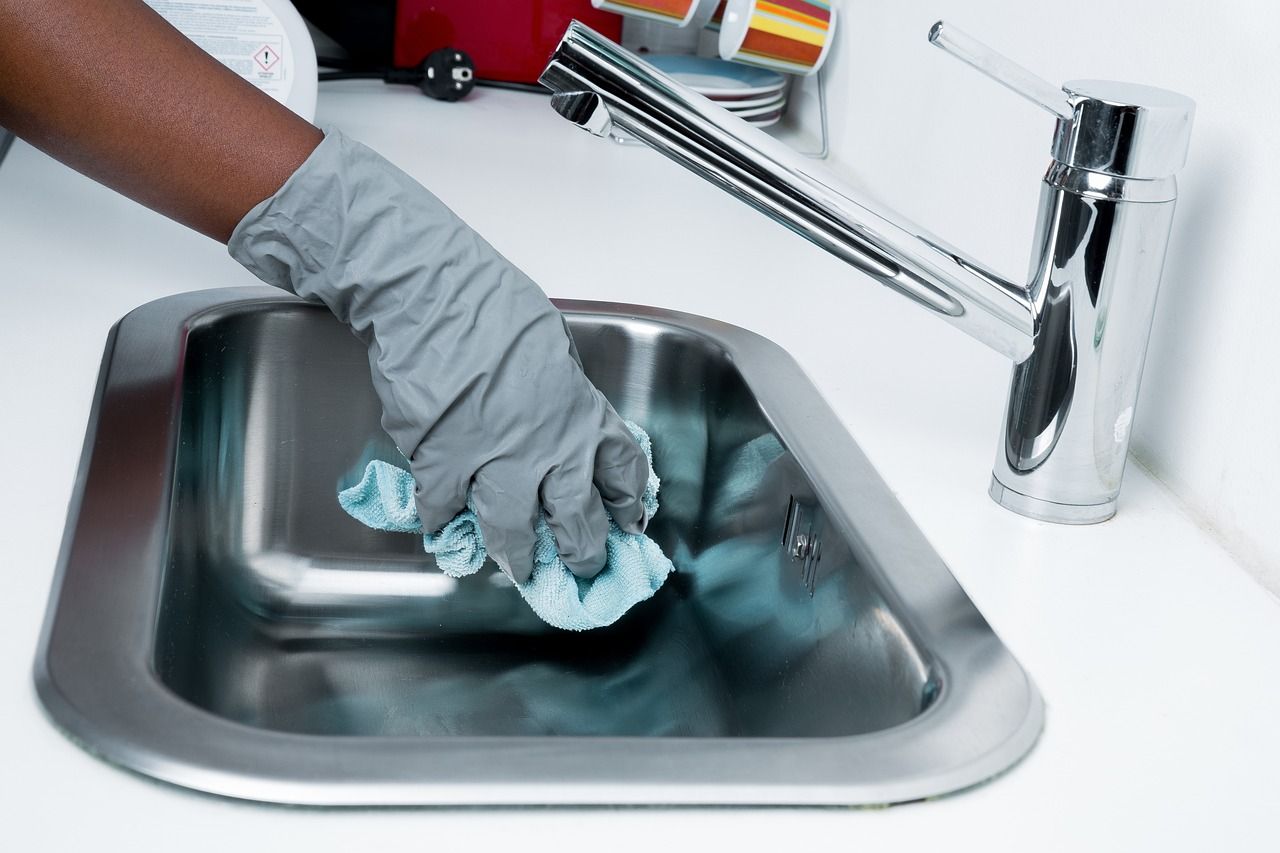
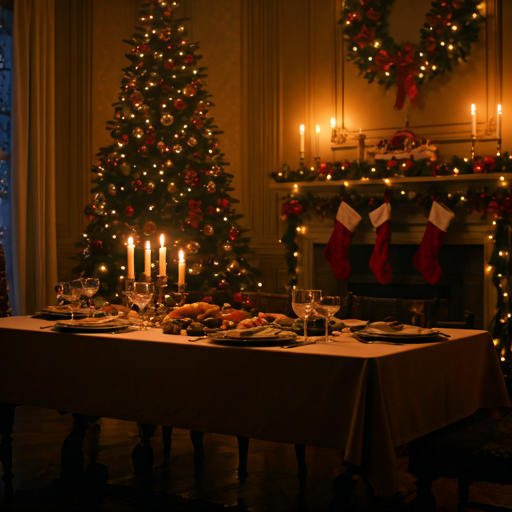
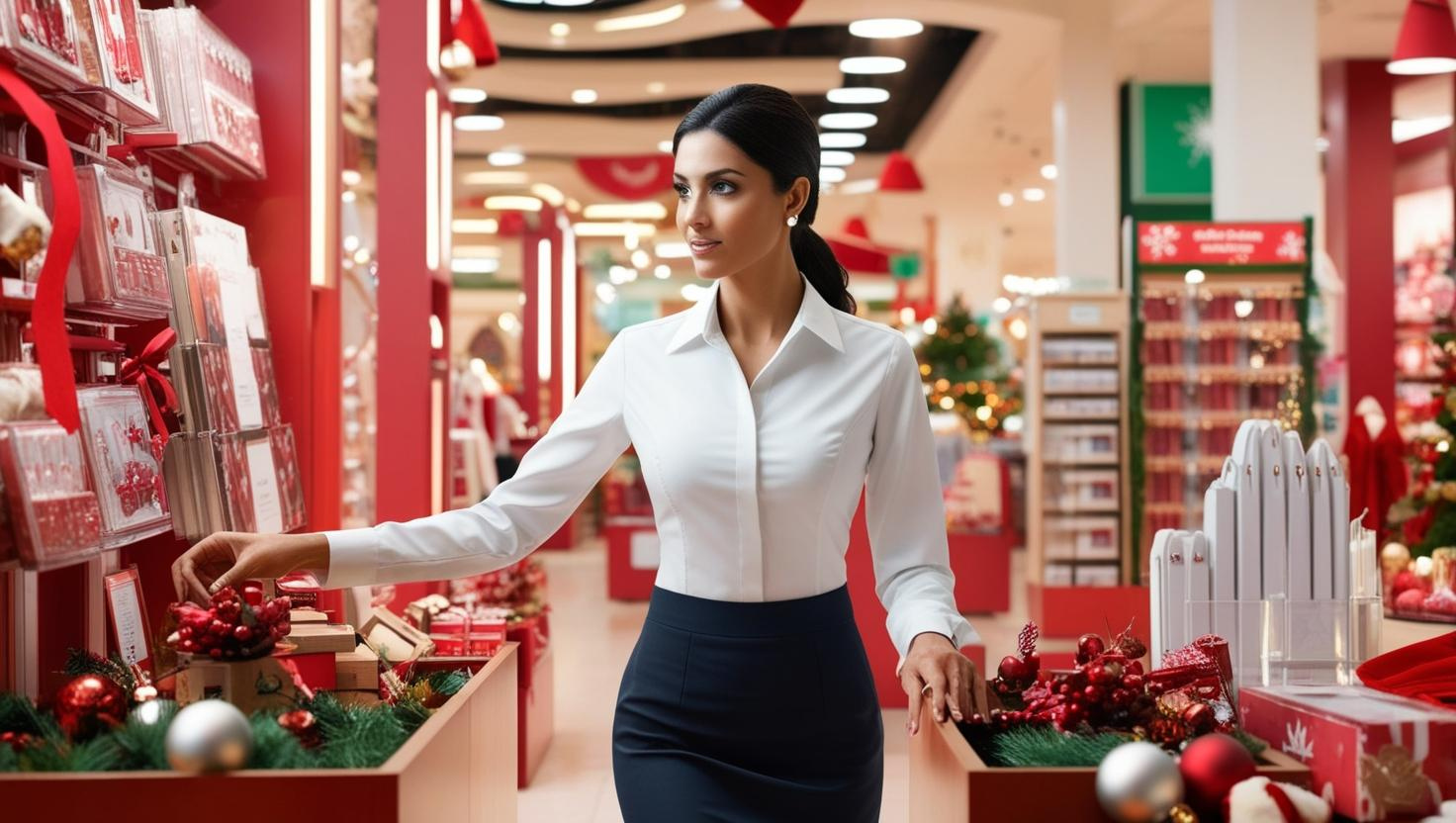
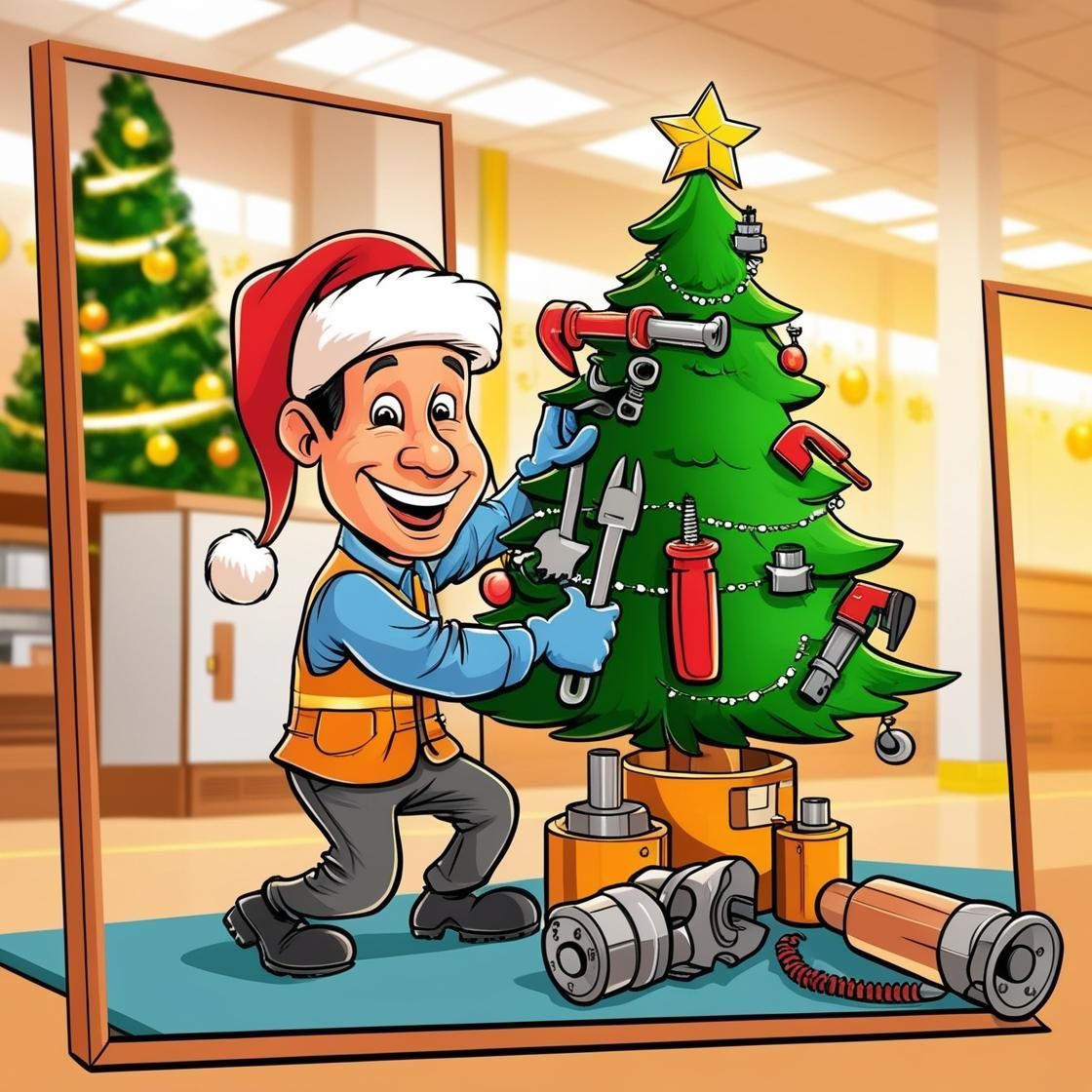
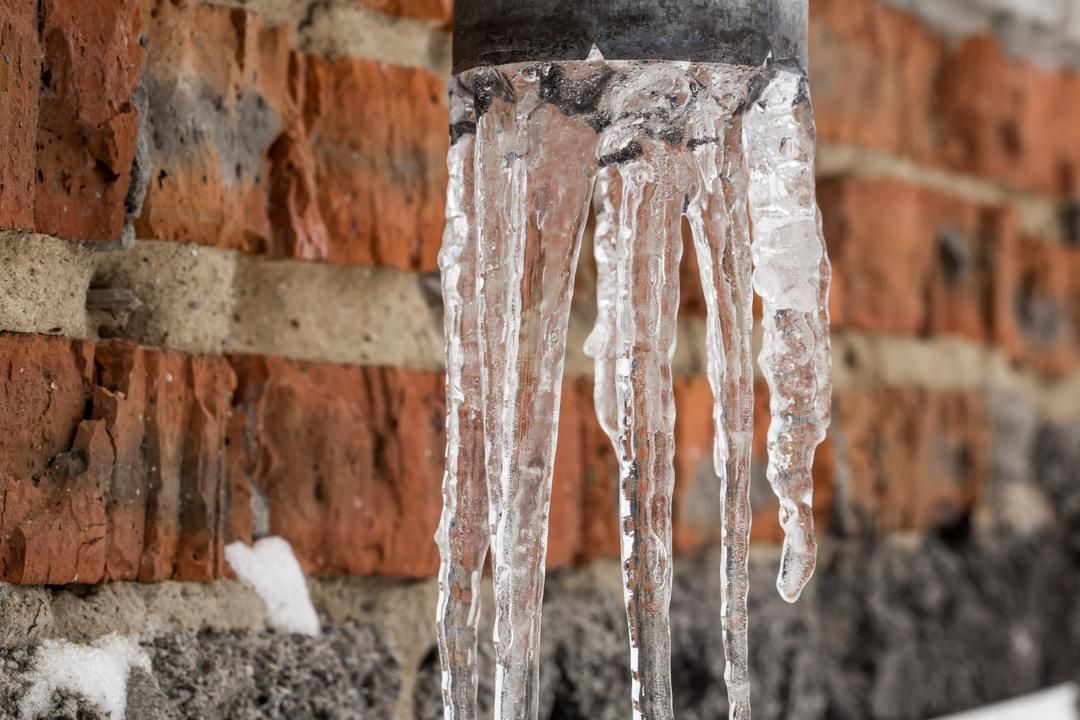